Hardwicks Meats processing site, Kyneton, Victoria
- hellolaurataylor
- Apr 7
- 9 min read

The Hardwicks Meatworks site at Kyneton, part of Kilcoy Global Foods, has two main production lines designed to process both beef and lamb. Hot water is used on these lines for both cleaning and sterilising at various temperatures between around 42 °C (at which warm water is held) and the sterilising minimum of 82 °C.
Sterilising water is used primarily at the kill stations for continuous knife and utensil sterilising whilst lower temperature warm water is used for cleaning and hot wash down. The hot water streams are delivered by two ring mains supplied to both floors of the facility. While some meat processing plants have high-grade vent steam available to recover, this site does not have a rendering process so there is no steam produced.
Existing system
Heated water on the Hardwicks meat processing site had previously been supplied by a 2 MW gas boiler. The plan to replaced the boiler with a heat pump was driven from a desire to reduce reliance on fossil gas at the site and to enable the site to produce enough hot water to operate at levels to improve shelf life and access further export market growth. The boiler replacement was a part of a wider initiative to decarbonise the operation and reduce and control energy costs.
Heat pump solution
To deliver hot water at an average 75 °C to satisfy the majority of the heat demand for the 85 °C plant hot water circuit, a 1 MW (thermal) capacity high-lift ammonia heat pump and associated heat recovery infrastructure was specified. Once fully optimised, the heat pump and additional cooling oil heat recovery would replace gas as the base load thermal energy
supply. The system design also made use of existing thermal energy storage in the form of approximately 150,000 L hot water storage tanks to enable the 1 MW heat pump to build the base thermal requirements for the plant with final water temperatures provided by the
existing gas hot water heaters.
Whilst the existing main natural gas boiler had an output capacity of 2 MW, the 1 MW (thermal) to be provided by the heat pump will satisfy much of the load as it is designed to operate continuously during weekdays with the resultant pre heated water stored in a thermal storage tank at 75 °C preheat. The preheated water is then pumped to a second tank that is heated to the final temperature required by the plant (water heated to
85 °C to 88 °C) with final circuit water temperatures delivered at a minimum of 82 °C.
The heat pump would also reduce existing condenser and oil cooler loads on the central ammonia system by an estimated 800 kW thermal heat rejection with resulting savings in water and power used by condenser fans and refrigeration compressors.
Integration into two-stage ammonia refrigeration system
The high-lift ammonia heat pump was integrated into the plants existing high stage condensing circuit of the two-stage ammonia refrigeration system (effectively adding
a very high pressure third stage to the refrigeration circuit) to recover low-grade heat from the plant’s existing ammonia refrigeration systems and use it to generate process hot water at the site, replacing gas.
The heat pump elevates the temperature of the incoming cold-water supply to then provide hot water to two thermal storage tanks for subsequent use in the process hot water streams. Heat is also be recovered from oil cooling circuits of three existing refrigeration
screw compressors to further supplement process hot water thermal demand.
compression plant at the site.
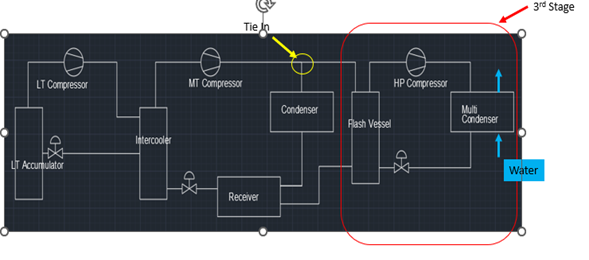
Project outcomes
The total project cost $2,577,000 including the high voltage upgrade, interface upgrades to the existing solar PV and battery system, as well as the costs for the heat pump and oil cooler heat recovery components. The heat pump-specific upgrades accounted for 56% of the total project costs, and included the heat pump skid, associated hydraulics, electricals, a new plant room and associated installation and commissioning costs required to fully install the system.
Currently the projected annual gas savings is 27,000 GJ based on current operating practice. Since installation the heat pump is found to have been operating for 65% of total hours in a year - considerably less than the 78% of total hours assumed in the business case. There is, however, potential to further modify the hot water inventory approach to achieve full savings originally projected.
Heat pump modifications
A number of modifications to the heat pump were made during and after commissioning, including:
Control pressure to ensure heat pump is favoured over cooling towers
Vibrations on the heat pump skid were rectified
Air lock in the oil cooling lines was rectified
Heating control of the compressor oil sump was rectified
Optimising control operation and mechanical piping to achieve full heat pump benefit
Oil cooling system modified to oil heat recovery system
Optimising control operation on the expansion valve and level probe
All distribution fluid pipes were insulated with 25mm of closed cell foil pipe insulation to minimise heat loss.
Heat pump performance
Projected annual reduction in gas reduction: 30,780 GJ (once fully operating as a base load during weekdays and heat storage build up on weekends).
Projected annual electricity increase: 1,107,043 kWh*
Associated annual CO2-e reduction: 883.3 tonnes
Heat recovery from oil coolers on compressors
Projected annual reduction in fossil gas by recovering heat from existing refrigeration compressors oil cooling circuits: 2,419 GJ
Associated annual CO2-e reduction: 124.2 tonnes
Upgrade to the electrical supply system
In addition to the heat pump installation, the project included a significant upgrade to the electrical supply system which sees the site becoming a high voltage customer, taking supply at 22 kV from the Powercor network and also upgrading total supply capacity from 2MVA to 4 MVA. This upgrade allows the heat pump and thermal storage tanks to be better integrated with the xisting on-site renewable energy supply infrastructure of 2.5 MW solar PV and a 2 MWh battery energy storage system (BESS).
Other benefits from the project
Potable water reduction in condenser.
Improved refrigeration condenser capacity available.
Reduced chemicals for condenser water treatment.
Potential to avoid future refrigeration condenser and gas boiler expansion requirements.
Potential to reduce imported power supply costs by demand management and load shifting strategies using available thermal storage inventories.
Project observations, findings and challenges
During the design, installation and commissioning phases of the project, a number of observations and findings were made and challenges encountered and overcome:
Existing thermal storage of 150 kL in two adjacent tanks enabled a 1 MW heat pump to be installed. Had these not been available the capital expenditure would have been higher, so was an important factor in the project development.
The heat source from the condensers needed to match the process heat demand. That is, the heat pump extracts 800 kW from refrigeration circuits which is less that total heat rejection. This heat extraction saves water and condenser fan costs and therefore significantly contributors to the overall system co-efficient of performance delivered.
High-temperature heat pump technologies have improved significantly in recent years allowing capital costs to be more competitive.
There was complexity in control to handle hot water inventory (i.e. constant supply from heat pump and variable plant demand).
Power infrastructure needed to be considered if the incremental power demand for heat pump caused capacity issues.
When evaluating a heat pump for preheat applications overall benefits to the wider system and operations need to be considered, in addition to gas savings.
Operational risks need to be considered. While the 85+ °C water required by the plant could have been delivered by the specified heat pump, it would have needed to run at much higher head pressures. Instead, to minimise risk, it was proposed to preheat the water to between 70 °C and 75 °C and use the gas to do the final heating to take it to 85+ °C.
It was critical in delivery of this project to include commissioning plans due to the requirement to integrate various upgrades (heat pump, refrigeration heat recovery, thermal storage, high voltage upgrades and interface into renewables, etc.).
The chosen heat pump employs a variable speed drive in conjunction with a high-pressure multistage reciprocating compressor. This allows for high efficiency at part-load demands and to match the thermal load more effectively. It can also be used to reduce site electrical peak demand during high demand periods. The system also uses a combination of multistage pumps and modern e-motor drives to minimise power used to convey process hot water over the system. Whilst there needs to be more tuning to optimise these, it’s believed the decision to incorporate these technologies into the original design will allow the site to be more flexible in how and when hot water is produced from this system.
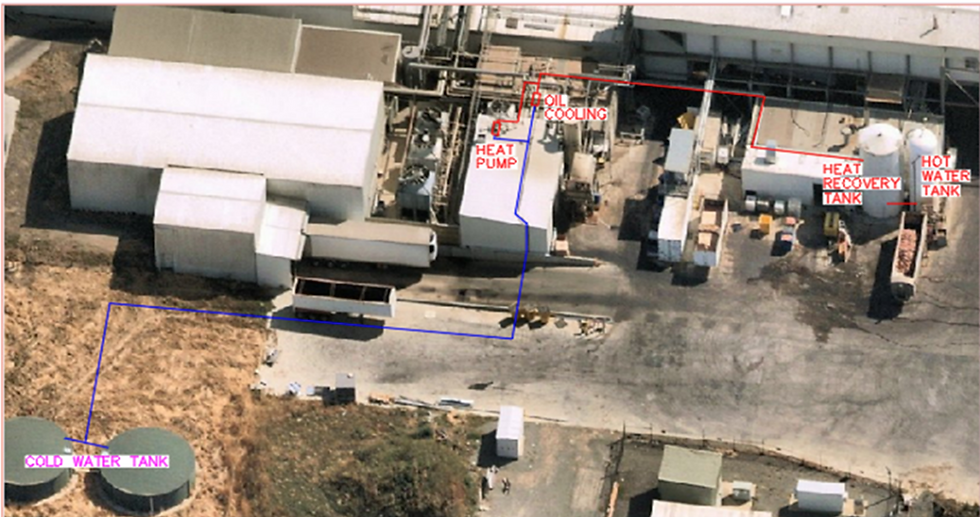
Although the heat pump’s power demand is reasonably high, the variable speed invertor drive has helped in minimising the peak demand the system sees on start-up. Whilst for this site the power upgrade was required to facilitate the load and improve the solar PV system interface, at other sites there may be potential to avoid power upgrades through site supply reconfiguration as well as controlled start-ups to avoid excessive load demands. The selection of the variable speed drive on the heat pump – as well as the water supply pump – provides the system with very good flexibility and ensures good part-load performance. It also reduces capital as it avoids multiple compressor costs and associated complexity in sequencing.
Because this heat pump uses condenser water (from main site ammonia system) as its heat source, the thermal performance is not substantially impacted by ambient conditions. The heat pump will ,however, operate more effectively during the warmer months due to warmer supply water temperatures as well as higher loading on condenser systems from which it sources its low-grade. This results in lower temperature lift during summer than winter periods.
Given the system uses a flammable and toxic refrigerant (ammonia), safety monitoring systems needed to be incorporated into the new compressor room. For future applications where the heat pump systems are co-located into existing refrigeration rooms which already have refrigerant safety systems, the extra costs of a safety system can be avoided.
Like other heat pumps, the coefficient of performance (COP) of this compressor is reduced at high delivery temperatures. However, it was found that the 74 °C to 75 °C current target temperature for the process water preheat is a good compromise for current hot water demands (i.e., higher water flows and lower delta T for the heat exchangers).
The lubrication of the heat pump is also a consideration in final selection of operating temperatures and consequent process water flows through the heat pump’s heat exchanger. As operating temperatures increase normally, available lubricating oils can become too viscous at source temperatures or too thin at sink temperatures, which can diminish its chemical stability. Lubrication oil condition is being closely monitored by Hoctor Refrigeration as the operating parameters (e.g., head pressures, temperature lift and water flows) are varied.
The thermal storage component of this project has been crucial in delivery of a viable heat pump system in a meat processing plant. Whilst this was expected, the project has demonstrated that it can be practically delivered in this type of complex plant.
The design of the supply water system in combination with the thermal store (preheat tank) ensures the maximum temperature lift over the heat pump heat exchanger is achieved (cold water in/preheat water out). Ideally this approach should be used as it maximises lift over the heat pump which then delivers higher COPs and efficiencies.
Because existing hot water tanks were used in the pre-heating system, they were not designed specifically to exploit stratification effects. It was possible, however, to place the inlets and outlets in both the pre-heat and final heat tanks to exploit heat stratification but still allow flexibility in fill rates and water inventory held. Also, as this is a once-through system, it guarantees the maximum water temperature lift, thus reducing the requirement to finely balance water temperature stratification over the height of the tank as would be the case if warm water was returned back through the heat pump heat exchanger.
As the heat energy supplied from the heat pump is more expensive than the heat recovered from the refrigeration oil cooling heat exchangers – as well as the existing desuperheater – the sequencing has been introduced to ensure these other sources of heat are recovered prior to the heat pump. In this case there is normally sufficient heat load required to utilise heat available from all of these including the heat pump.
The relative gas and power costs can significantly impact the financial viability of the heat pump project. In this project the financial benefits and associated life cycle costs for heat pump installed appears to be better than expected due to higher projected natural gas costs than originally assumed.
Project summary
Location: Kyneton, Victoria, Australia
Facility type: Meat processing
Heat pump supplier: Mayekawa Mycom
Installer: Hoctor Refrigeration
Consultant: Energy & Thermal Services
Equipment replaced: 2 MW gas boiler
Water temperature set point: 75 °C
New equipment: 1 MW ammonia heat pump
Estimated annual gas savings: 30,780 GJ
Estimated annual emission savings: 883 t CO2-e
Total project cost: A$2,577,000
Project payback: five to eight years
This case study was delivered with support from RACE for 2030.
* Net change in power consumed by the heat pump compressor minus resultant savings in refrigeration and condenser power systems. Note that the energy cost saving benefits was originally based on a gas price of $12/GJ. Gas prices have significantly increased since then with delivered prices in Victoria $18 to $20/GJ at the time of this case study’s development and publication.